2009 Pegasus Warehouse Expansion
Planning for our warehouse addition began in early 2008, before the economy took a turn for the worse. Our warehouse was bursting at the seams and the lack of adequate space was hampering optimal efficiency. Having more room in our warehouse would also allow new product lines to be added to our inventory. We decided to go ahead with our expansion, despite the difficult economy. The economic slowdown actually resulted in lower prices for many building materials. The various subcontractors also submitted very competitive bids. We believe that we got much more for our money than we would have a year earlier. Our addition will add approximately 10,000 square feet of warehouse space. Our parking lot will also be expanded.
![]() |
Circa May 1990When we moved into our new building in 1990, we only needed a fraction of the available space. We knew it would be a long time before we would need to expand. That's Debbie setting up shelving. She later became our office manager. During her 23 years with Pegasus, Debbie always went out of her way to help a customer in any way she could. Sadly, Debbie passed away unexpectedly on July 18, 2011. We miss her. |
![]() |
April 15, 2009Even though we had more than enough building space back in 1990, we purchased enough land to allow future expansion. Today we're glad we did. We prefer to double the size of our current warehouse rather than having to move the whole business. On April 15th, silt fencing was installed for erosion control. |
![]() |
April 28, 2009 - 7AMGround breaking day. Starting to strip away all of the topsoil from the building pad area as well as the area that will be used for an expanded parking lot. |
![]() |
April 28, 2009 - 5PMBy the end of the day, all of topsoil has been stripped and the subsoil compacted with a vibratory roller. As you can see, the land slopes down quite a bit. We're going need about 300 dump truck loads of fill. |
![]() |
April 29, 2009Starting to bring in fill. Luckily, there are a couple of road construction projects nearby that need to get rid of excess fill. We're able to get all the fill we need for a price that can't be beat! A soil test engineer will insure that the fill is of good quality and properly compacted every 8 to 12 inches. The large pile in the background contains the topsoil that was stripped the previous day. |
![]() |
May 8, 2009Many loads of fill have been delivered. Some of the fill had to be stockpiled on our parking lot while other fill was spread out to dry after recent heavy rains. |
![]() |
May 15, 2009Getting ready to pour footings. This detail shows how the foundation for the addition is tied into the foundation of the original building. |
![]() |
May 15, 2009The foundation steps down due to the slope of our lot. |
![]() |
May 15, 2009First concrete being poured. |
![]() |
May 15, 2009Block being delivered. |
![]() |
May 18, 2009Forms have been removed from the footings. |
![]() |
May 18, 2009Starting to lay foundation block. |
![]() |
May 22, 2009To make sure that our business (including our website) can continue to function during a power failure, we're installing a 60KW automatic, natural gas powered backup generator. This is the generator mounting pad. |
![]() |
May 26, 2009The masons have set 14 courses of block around most of the perimeter. This still doesn't quite get us up to the finished floor level! We're going to need many more loads of fill to get the inside grade ready to pour the floor slab. |
![]() |
May 26, 2009Another view of the foundation wall. Again, this still doesn't quite get us up to the floor level. |
![]() |
May 29, 2009Using a Hydro-Lift scaffolding system, the block walls should be rising fairly quickly. More fill is being brought in to build up the grade within the building perimeter. |
![]() |
June 4, 2009The generator has been installed on its pad. This 60KW unit is powered by a 350CID Small Block Chevy engine that is fueled by natural gas. It should have plenty of capacity to power our entire building during utility power outages. |
![]() |
June 5, 2009Quite a bit progress on the walls has been made during the week just ended. |
![]() |
June 17, 2009The masons have completed their work on the exterior walls. |
![]() |
June 17, 2009The north wall will include an additional loading dock door. The stub walls are for a dumpster enclosure. |
![]() |
June 25, 2009A large mobile crane showed up on the morning of June 25th. By the end of the day, all of the large pieces of the roof structure were in place. |
![]() |
June 30, 2009The roof decking is being installed. The steel workers should have their work completed within a few days. |
![]() |
July 3, 2009The roof was insulated and the rubber membrane was installed today. |
![]() |
July 6, 2009A two-part expanding foam insulation material is being injected into the walls. |
![]() |
July 9, 2009 - 9AMThe first half of the floor slab is being poured today. A laser level is attached to the steel column. In the background is the laser guided screed which helps produce a very flat floor slab. |
![]() |
July 9, 2009 - 5PMBy the end of the day, the first half of the floor slab is completed including sawing control joints. A crew will be here in the evening to apply a hi-tech silica surface treatment to provide a very hard, long-wearing finish. The second half of the floor has been prepared for pouring the following morning. |
![]() |
July 24, 2009Steady progress is being made on electric, HVAC, sprinkler system, security system, dock leveler, overhead doors and other interior details. The sodium light fixtures shown here are just temporary work lights. |
![]() |
July 28, 2009The painters have been busy on the exterior. The existing building received a new roof, masonry repairs and a fresh coat of paint. It now blends well with the 100 foot long addition. |
![]() |
August 7, 2009The painters have started on the interior. Everything including the roof deck and steel joists will be painted white to help brighten the space. |
![]() |
August 10, 2009Our expanded parking lot is being paved today. The larger lot not only adds parking spaces, it also allows even the longest, 53 foot semi trailers easy access our loading dock. |
![]() |
August 11, 2009The parking lot looks great, but it will be a few days until we can use it. The warm August weather increases curing time. |
![]() |
August 19, 2009Just a few more details need to be taken care of on the interior. We hope to have an occupancy permit within a few days. |
![]() |
August 19, 2009The wall that separated the addition from our existing warehouse has been removed. The pallet racks seen in this photo will be moved as soon as we receive the occupancy permit. |
![]() |
August 26, 2009We've started to assemble shelves. It's going to take a while to get all of the shelving and pallet racking assembled and stocked. The building contractor still has a few details to take care of but the major construction tasks are now complete. |
![]() |
January 15, 2010It has taken several months to gradually rearrange the warehouse while maintaining our usual same-day shipping schedule. We're still not done, but we're getting close. Our packing and shipping department will be moving into the area near the fork lift in this photo. |
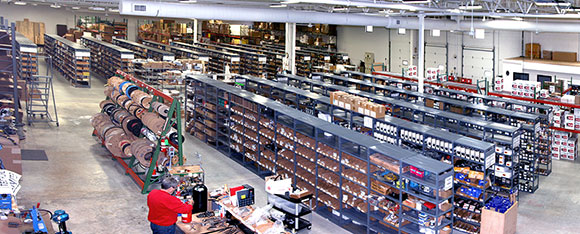
October 28, 2010
We're getting settled in after about a year. This photo shows a portion of our expanded warehouse. In the foreground, Jim is filling a fire extinguisher bottle. Beyond Jim is a heavy-duty reel rack holding some of our bulk hose inventory. In the background (barely visible) is a large area of pallet racking with enough capacity to store 240 pallets loaded with bulky items. Our loading docks are visible in the upper right portion of the photo. There is still work to be done. We are working on a variety of projects to make the warehouse even more efficient. This will enable us to continue to provide the high level of service that our customers have come to expect, even while handling an increasing number of orders each day.
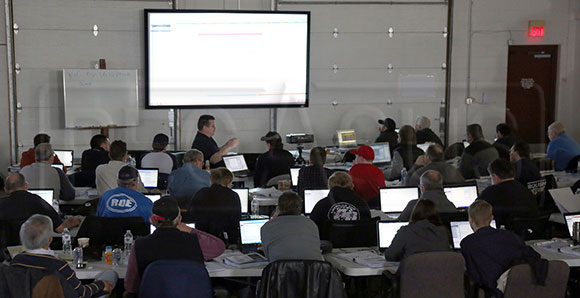
March 21, 2015
Having a large shipping and receiving area allows us to host special events such as our annual AiM Data Acquisition Seminar. For the past five years Roger Caddell, official trainer for AiM Sports, has brought his years of experience to our New Berlin Wisconsin location. Roger's seminars are interesting, entertaining and informative.